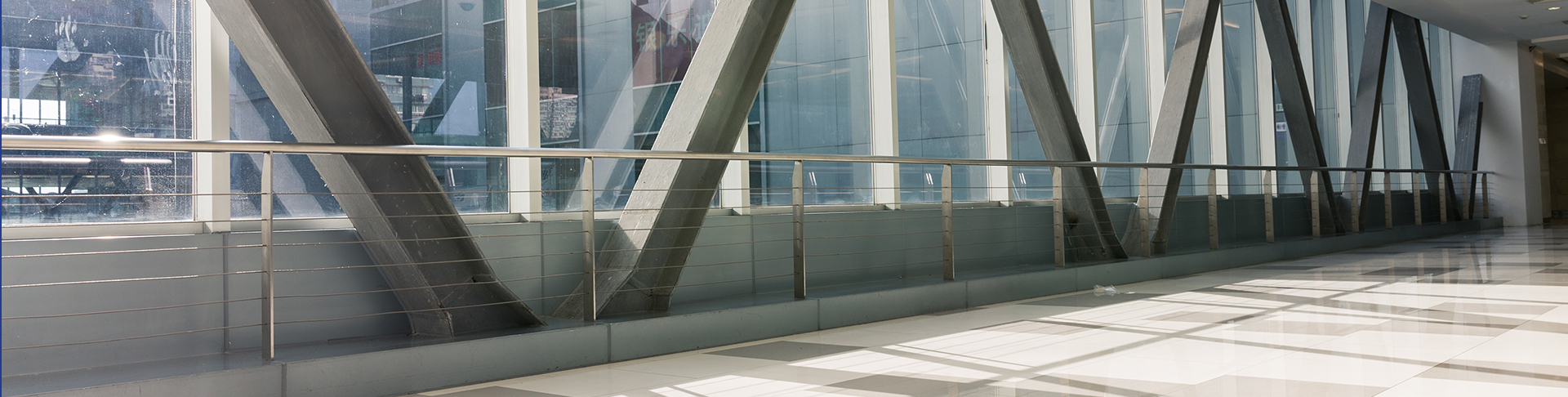
Quality Data Series · Product Quality Inspection
Quality supervision, strict control
Industry Overview
Quality inspection is also called "technical inspection", that is a quality management method to judge whether the product or batch is qualified or not by comparing the specified quality standard with the quality characteristics testing results generated by certain inspection and testing methods and measures. The intent is to ensure that unqualified raw materials fail to be put into production, unqualified parts will not be transferred to the next process and unqualified products will not be shipped. Additionally, the data reflecting quality status will also be collected and accumulated, providing reference for measuring and analyzing process capabilities, monitoring processes and improving quality.
At present, the commodity quality inspection is mainly in the charge of relevant government sectors, production units and the third-party inspection and testing institutions which conduct quality supervision and control over every step of the production and circulation of goods. As a testing organization, various activities including spot checks, inspection and testing, report issuance and quality management, etc., require a whole set of architecture and information system to support the efficient operation of daily work. The product quality inspection integrated platform provides comprehensive and rigorous business management for the daily work of such laboratories.


-
Comprehensively construct a standardized database and improve the data transverse longitudinal integ
Form standardized management of data about personnel, equipment, standard articles, methods, samples, appliances and qualification.
Lay a solid foundation for data integration. -
Improve customers' service capacity and realize balanced management efficiency
Unify customer resources, information and service standards, improve the service level, increase customer adhesion and improve customers' loyalty.
Realize customer data sharing by multiple channels and support cross-business, diversified and coordinated services.
Establish an integrated customer service system, give quick response to customers, explore customers' values and explore business innovatively.
Establish self-service channels for customers to improve the working efficiency and the capacity of giving quick response to customers. -
Realize efficient operation of intelligent and digital labs
Realize whole-process and all-round coverage of testing business, including testing and spot check outside factory, improving working efficiency.
Realize time fragmentation management and establish channels for quick approval and review.
Realize all-round informatization management of lab work: improve the normalization degree of inspection business, avoid the randomness of manual operation, and make inspection work traceable.
Realize automatic instrument data capture, improve work efficiency and mitigate workload.
Realize automatic generation of inspection reports and improve work efficiency.
Realize all-round management of lab quality assurance and quality control.
Provide accurate and scientific supporting bases for management decision making by virtue of statistical decision-making analysis.